OEM 맞춤형 고정밀 프로그레시브 펀칭 딥 드로잉 몰드 주조 및 판금 몰드 스탬핑 다이 툴링
동영상
기능
연속 다이라고도 하는 프로그레시브 다이에는 2개 이상의 스테이션이 있으며 서로 다른 스테이션에서 2개 이상의 스탬핑 프로세스를 완료할 수 있습니다.
응용 분야
자동차 부품을 위한 자동차 산업.
자동차 생산 라인 생산 능력이 향상됩니다.
제품 세부 정보
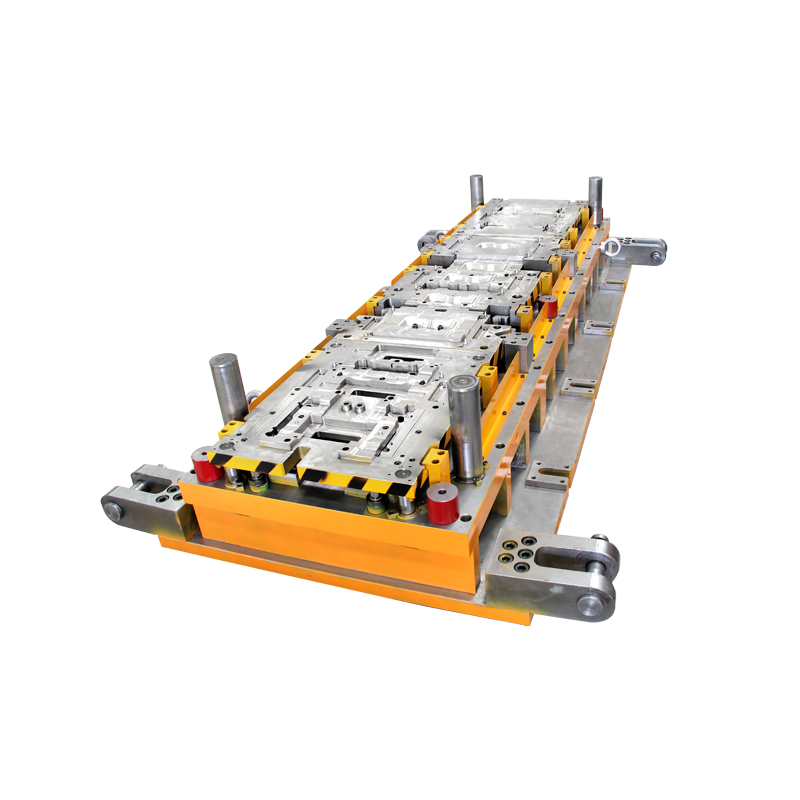
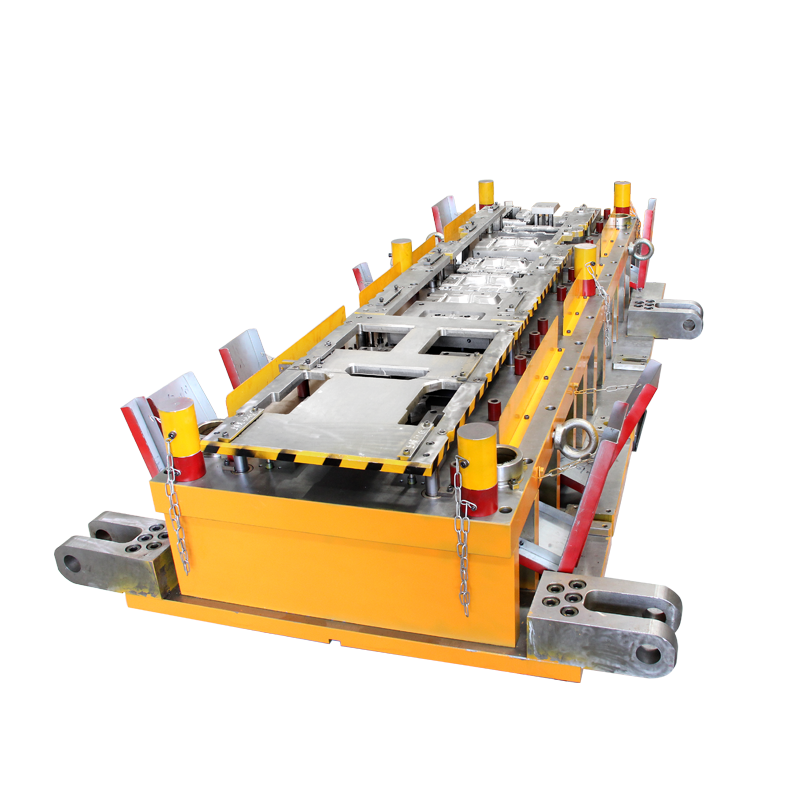
자세한 소개
다이 설계 작업의 기본 요구 사항은 다음과 같습니다. 다이 설계는 모양 및 크기 요구 사항에 따라 도면에서 나온 부품, 다이 구조가 간단하고 확고한 설치, 편리한 유지 보수, 내구성을 보장해야합니다.작동하기 쉽고 안전하고 신뢰할 수 있는 작업;제작이 쉽고 가격이 저렴합니다.
다이 설계의 일반적인 단계
먼저 필요한 정보를 수집하고 스탬핑 프로세스를 분석합니다.포함: 부품의 모양, 크기, 정밀도 요구 사항 및 조립 관계에 대한 완전한 보기, 기술 요구 사항 명확한 도면 또는 샘플이 있어야 하며 포괄적인 이해가 있어야 합니다.부품 스탬핑 프로세스 카드(일반적으로 스탬핑 기술자가 제공)를 이해하여 이전과 이후를 연구합니다.프로세스 간의 관계와 처리 프로세스 요구 사항은 프로세스 간에 상호 보장되어야 하며 다이의 수와 유형은 프로세스 카드에 지정된 프로세스 계획에 따라 결정되어야 합니다.금형 구조를 결정하기 위해 부품의 생산 특성(시험 생산 또는 배치 또는 대량 생산)을 마스터하고 간단한 금형 또는 더 복잡한 고생산성 금형을 사용합니다.판재 또는 스트립재, 롤재 또는 스크랩재와 같은 구성재의 특성, 크기 및 공급 방법을 이해합니다.프레스 및 관련 기술 사양을 이해하고 선택한 장비에 따라 금형의 언로딩 방법 및 기타 보조 절차를 결정합니다.
금형 제조의 기술적인 힘, 장비 조건 및 가공 기술을 이해하여 금형의 구조를 결정하는 기초를 제공합니다.이러한 데이터에 대한 연구와 이해를 바탕으로 스탬핑 프로세스가 열악한 것으로 밝혀지면 성능에 영향을 미치지 않는 경우 처리 수정을 용이하게 하여 제품 디자인, 스탬핑 보다 완벽한 효과를 얻기 위해 더 나은 조합 사이의 공정 준비, 금형 설계 및 금형 제조.
둘째, 기술 및 경제적 부분이 보다 합리적인 스탬핑 공정 방식인지 결정합니다.부품의 모양, 치수 정확도, 프로세스 분석을 위한 표면 품질 요구 사항에 따라 블랭킹, 펀칭, 벤딩 및 기타 기본 프로세스와 같은 기본 프로세스의 특성을 결정합니다(이 간단한 프로세스 특성은 일반적으로 요구 사항에서 직접 얻을 수 있습니다. > 결정할 부품 차트의 >; 인발 시간 등과 같은 공정 수를 결정하기 위한 공정 계산에 따라; 각 공정의 변형 특성에 따라, 공정 배열의 순서를 결정하기 위한 크기 요구 사항에 따라, 첫 번째 펀칭인 경우 펀칭 후 굽힘 또는 굽힘 후; 복합 스탬핑 공정, 연속 스탬핑 공정 등과 같은 공정 조합을 결정하는 생산 배치 및 조건에 따라
셋째, 금형 형태의 선택입니다.공정의 특성, 순서 및 공정의 조합이 결정될 때, 즉 스탬핑 공정 방식을 결정하려면 이때 금형 구조 형태의 공정도 결정해야 합니다(금형 선택은 다음 설명 참조). .
넷째, 필요한 프로세스 계산.주로 다음을 포함합니다: 블랭크 크기 계산, 가장 경제적인 원칙과 재료 사용의 합리적인 결정에 따라 샘플을 배열하기 위해;프레스를 결정하기 위해 펀칭 압력(펀칭력, 굽힘력, 인장력, 제하력, 미는 힘, 블랭크 홀더 힘 등 포함)을 계산합니다.편심 하중에 의해 다이의 품질에 영향을 미치지 않도록 다이의 압력 중심을 계산하십시오.금형의 주요 부분(오목 다이, 펀치 고정판, 패드, 펀치 등) 치수와 방전 고무 또는 스프링의 자유 높이를 계산하거나 추정합니다.볼록 및 오목 다이의 클리어런스를 결정하고 볼록 및 오목 다이 작업 부품의 크기를 계산하십시오.블랭크 홀더가 드로잉 다이, 드로잉 수 및 중간에 사용되는지 여부를 결정합니다.공정 금형 크기 분포 및 반제품 크기 계산.
다섯째, 금형의 전반적인 디자인.위의 분석 및 계산을 기반으로 전체 금형 설계를 수행할 수 있습니다.일반적으로 먼저 구조를 스케치하고 금형의 닫힘 높이를 미리 계산하고 금형의 형상 크기를 대략적으로 결정합니다.이때 각 구성요소의 구조를 설계하여 개략적인 방안을 결정할 수 있다.이러한 단계는 최상의 솔루션을 결정하기 위해 서로 밀접하게 연결되고 통합되며 보완된다는 점에 유의해야 합니다.일반적으로 전체 설계는 부품 구조의 설계를 고려하면서 이루어집니다.순서가 절대적인 것은 아닙니다.구성 요소 구조 설계에는 주로 다음 내용이 포함됩니다.
① 작동 부품.펀치, 오목 다이 및 볼록 및 오목 다이 및 기타 구조적 형태와 같은 일체형, 결합 또는 상감 및 고정 형태 결정입니다.
② 부품을 찾습니다.포지셔닝 플레이트, 배플 핀(고정 또는 이동) 등의 사용과 같이 그 형태는 다양하며 특정 상황에 따라 선택하거나 설계할 수 있습니다.프로그레시브 다이의 경우 초기 배플 핀, 가이드 핀 및 거리 펀치(측면 가장자리)를 사용할지 여부도 고려하십시오.
③ 하역 및 미는 장치.언로딩은 일반적으로 강성과 유연성의 두 가지 형태로 사용됩니다.단단한 인쇄 재료는 일반적으로 고정 언로드 플레이트의 구조 형태를 채택하고 유연한 언로드 재료는 일반적으로 스킨 또는 스프링을 탄성 요소로 채택합니다(스프링 또는 고무는 설계 및 계산이 필요함).
④ 가이드 부품.가이드부가 필요한지, 어떤 형태의 가이드부가 사용되는지 등을 포함한다.가이드 포스트 · 가이드를 사용하는 경우 가이드 포스트의 직경과 길이를 결정해야 합니다.
⑤ 거푸집 틀의 선정 및 설치 및 고정.
여섯째, 언론을 선택하라.프레스의 선택은 금형 설계의 중요한 부분이며 금형 설계 시 프레스의 종류와 사양을 결정해야 합니다.프레스 유형의 결정은 주로 스탬핑 공정의 요구 사항과 다이의 구조에 따라 달라집니다.
작업 흐름
1. 발주접수---->2. 디자인---->3. 도면/솔루션 확인---->4. 재료 준비---->5. CNC---->6. CMM---->6. 조립---->7. CMM-> 8. 검사---->9. (필요 시 3차 검사)---->10. (내부/고객 현장)---->11. 포장(나무상자)---->12. 배송
리드 타임 및 포장
3D 디자인 승인 후 45일
특송으로 5일: FedEx by Air
표준 수출 나무 케이스